Bristles.
Tools you will need:
From left to right; Jewelers Hammer, Flat Faced Hammer (any hammer with a moderately flat
striking surface will work fine), Metal Blocks ( or you can use the flat Anvil like surface that is
attached to a vice), 5" Snub-nosed Vice Grips, 5" Needle-nosed Vice Grips, Small pair of Pliers,
Pencil Torch ( any torch would work, I use this one because it will concentrate the heat to a
small area) and 4 Street Sweeper Bristles (2 long and 2 short). Tools that are not in the picture
that are used: Vice, Dremel/Grinder and files.
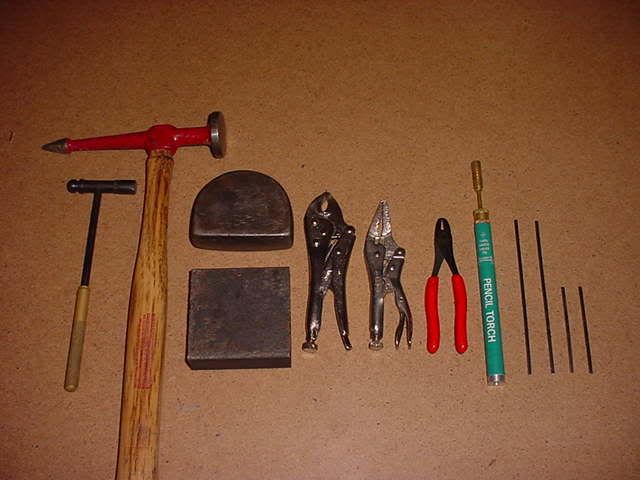
Set up torch in the vice or on a level surface to work on safely, grip one end of the bristle in vice grips
or pliers, then heat the opposite end about a half an inch from the end till it is red hot then bend to
a 45 degree angle.
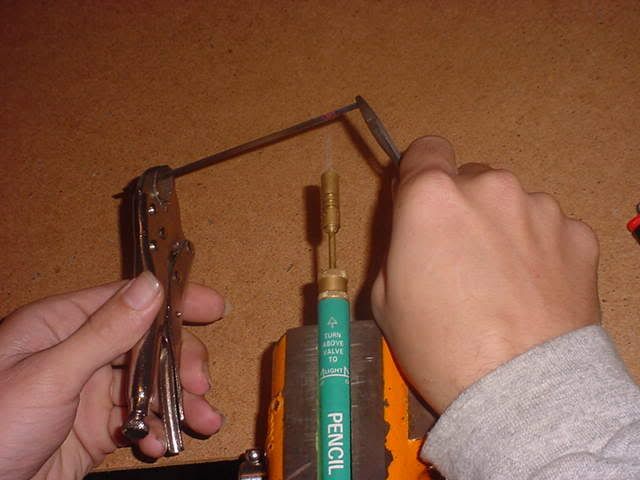
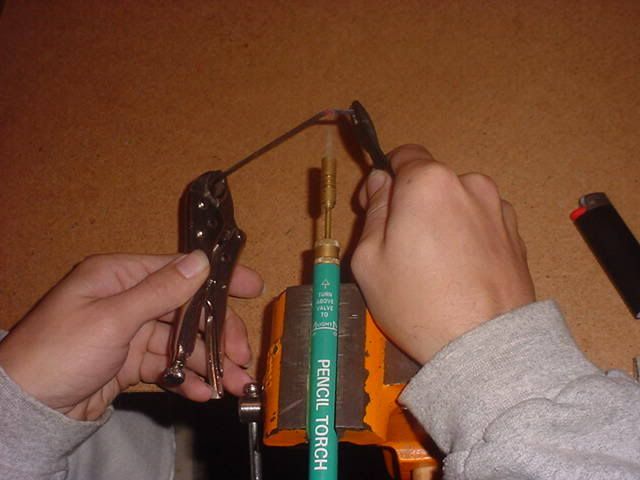
At this point, you will notice the bristle will start to buckle on the inside of the bend. Hammer
the bristle flat while red hot on a hard metal surface such as a metal block (Dolly) or the anvil
like surface on a vice. This is to stretch the outside of the curve while shrinking the inside curve
to create a nice bend while keeping the bristle flat.
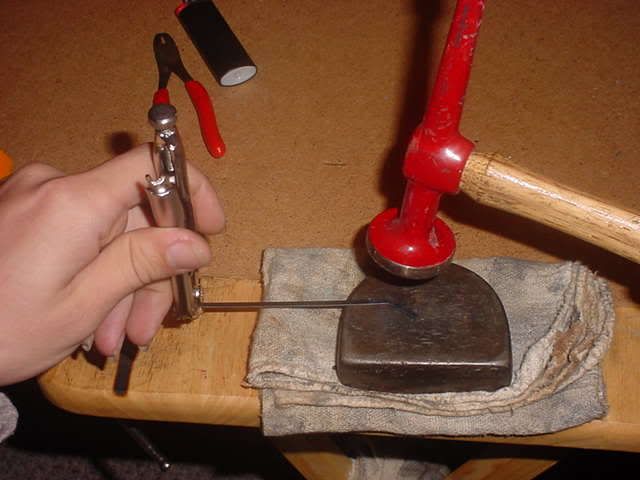
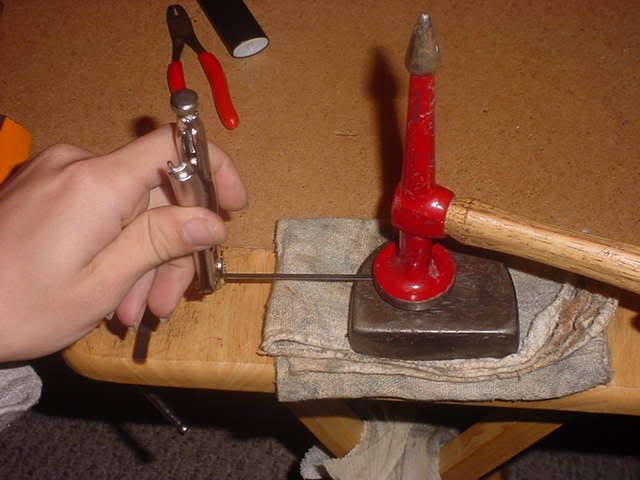
Repeat this process until a 90 degree angle is achieved. Do the other bristle the same way.
You should now have something that resembles the two bristles shown.
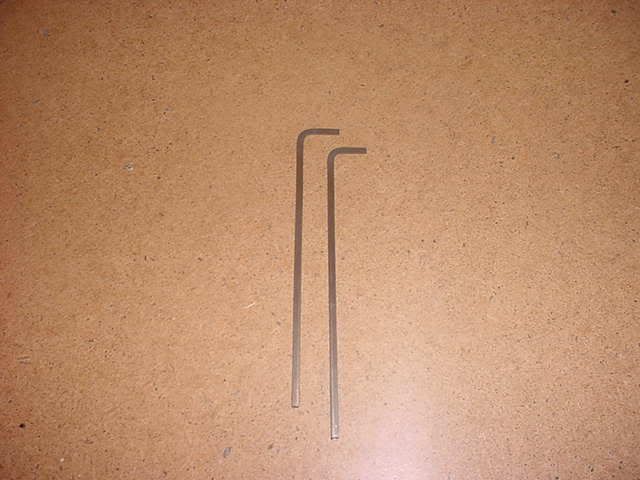
Once you have both bristles bent, clamp them both together with a pair of vice grips or pliers
and trim the ends with a Dremel tool or bench grinder, both the working end as well as the
bottom end. Trimming them together will insure an even cut of both pieces.
You will want to do this same step to the two smaller pieces that will become spacers for these
outside pieces. *Note: It is not necessary to use spacers, it is purely optional.
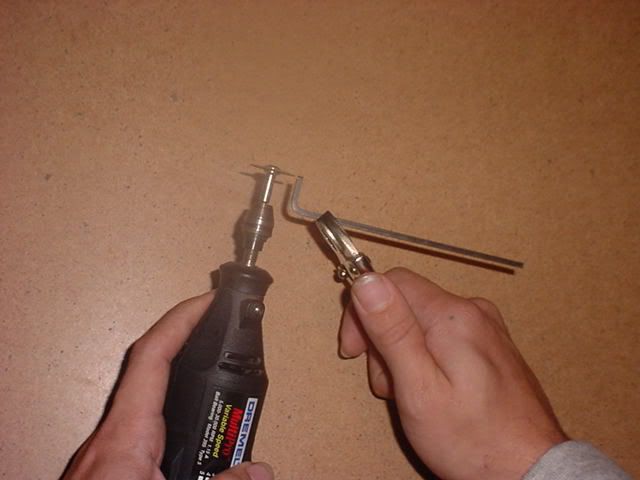
Now sand the outsides of each bristle to insure a good metal contact surface in between each
bristle and a small area on the edges about a half an inch from the bottom. The picture
may not show the area very well but is needed as this will be the area that will be welded.
Another area a half an inch from the top of the center (spacer) bristles of the other side will
need to be sanded or ground down so that there is a spot weld at the bottom of one side and
a spot weld at the top of the other side.
If you want to skip some steps just sand all the sides and edges of all four bristles then clamp
together for welding. *Note: Be sure to clean all areas before welding.
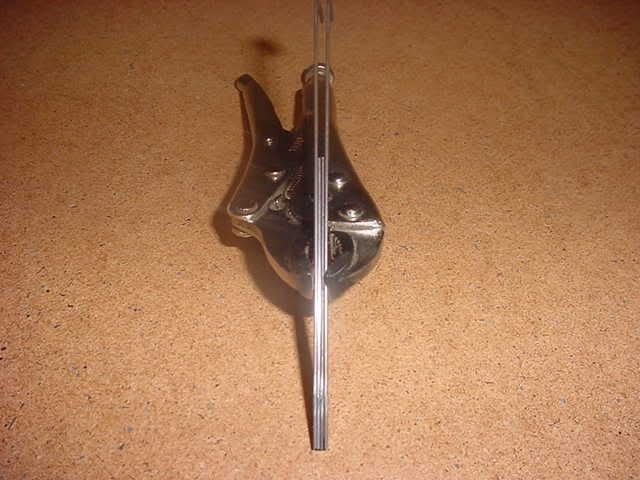
Now clamp the bristles together with a pair of vice grips on each side of the area to be welded.
Weld the edge of the four pieces together on both sides (one spot for each side). *Note: Be
sure to practice on a few bristles to get the wire speed and temperature settings adjusted or
these little babies will warp or just melt on you. *Note: If a welder is not accessible, any type of
2-part Epoxy (liquid or putty) such as JB Weld, Quick Steel or Milliput can be used to bond the surface
pieces together. Be sure to sand and clean the surfaces well before adhering.
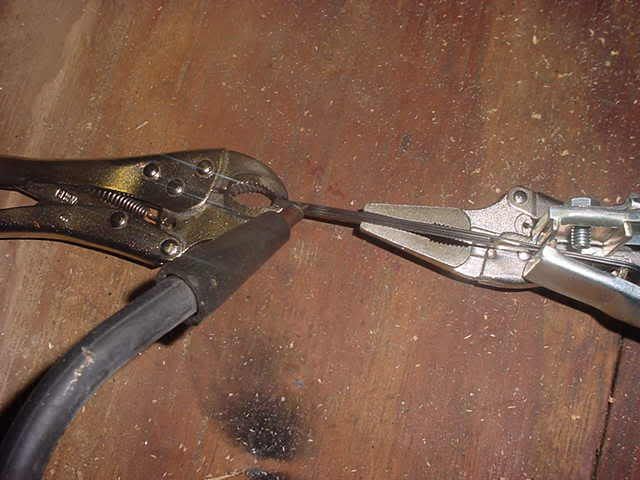
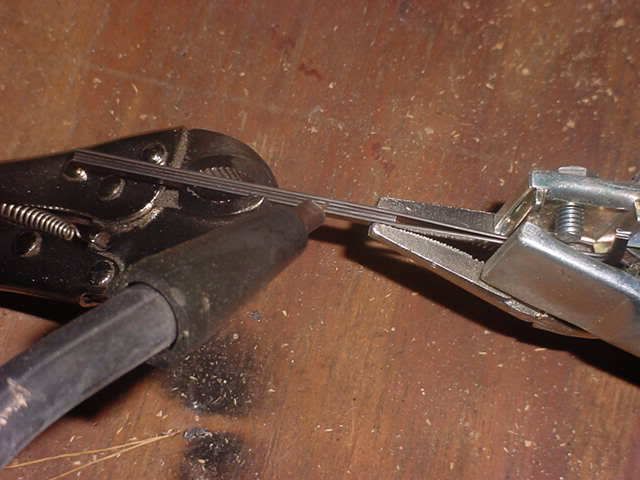
Now that it is all welded, grind the welds down so that the area is smooth and flat. Next put the
tension wrench in the vise where the center bristles are level with the top of the vice jaws and
spread the two outside (working end) pieces apart with a pieces of aluminum rod. A wooden
dowel rod or a pair of pliers will work as well.
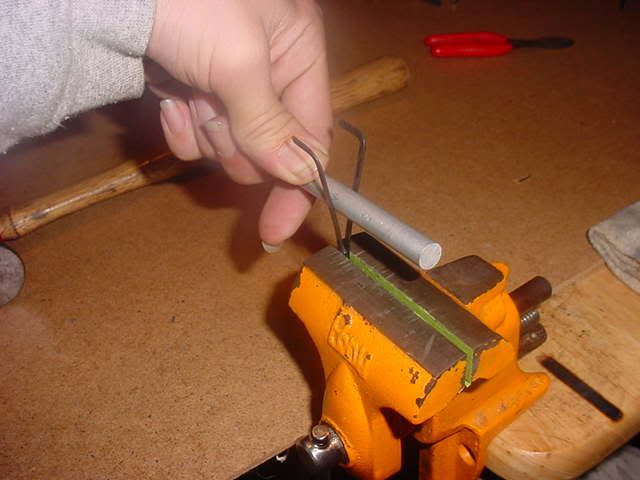
Now that the tension wrench is spread open you can now keep them sanded or coat them with
any color of enamel or urethane coating of your choice, then wrap a piece of 3/16" or 4.8 mm
heat shrink tubing around the bottom half or dip them in plastic coating for a smooth gripping
handle.
When all done, you should have something that looks like this.
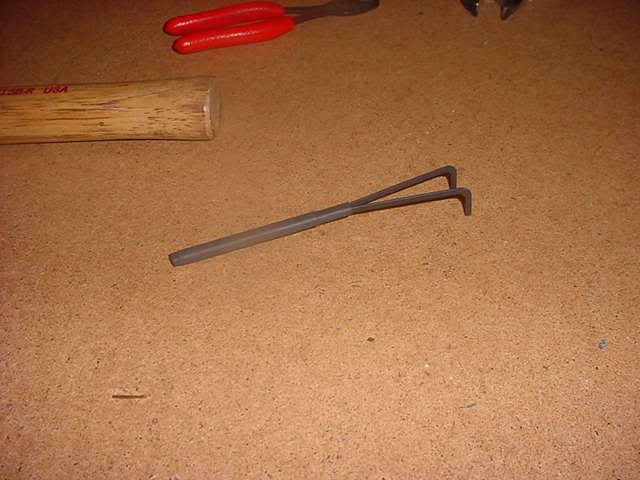
As a double bonus, this is how to make a flat serrated tension wrench using a street sweeper
bristle. One end is to be used in the bottom of the cylinder; the other end will be used for
top of the cylinder near the key pins.
While using the same bending method, bend one end in one direction and the
opposite end in the other direction.
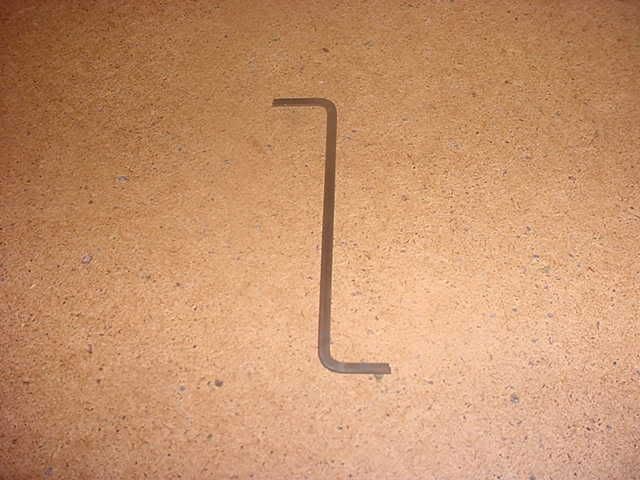
On the top of one end, file the round edge flat. This will be the area in which the teeth will be
filed into.
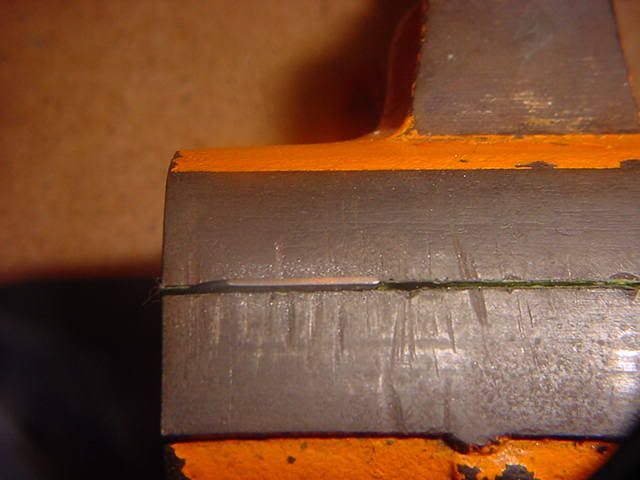
Use a square or triangle needle file to make 8 or 9 marks every 32nd of an inch. The marks made
will be where the valley of the teeth will be and the area between the marks will be the peaks or
tip of teeth will be. Be sure to file 3-4 strokes per mark to insure all valley's are the same depth.
*Note: If 9 marks are filed, there will be only 8 teeth, If 10 marks are filed there will be 9 teeth
and so on.
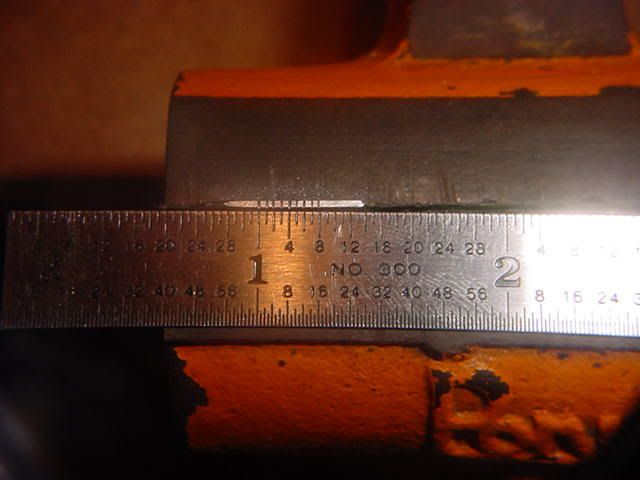
You should now have something that looks like this. Now file the flat area on the left
(based on this picture) lower than the teeth. This will make the teeth protrude and stick out
higher to grip the inside of the cylinder.
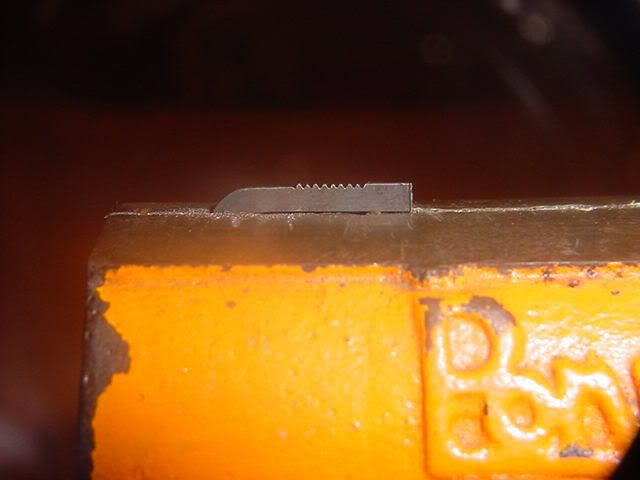
Now that the left side of the wrench is filed down, cut off the remainder of the bristle on the right
side at the peak of the nearest tooth.
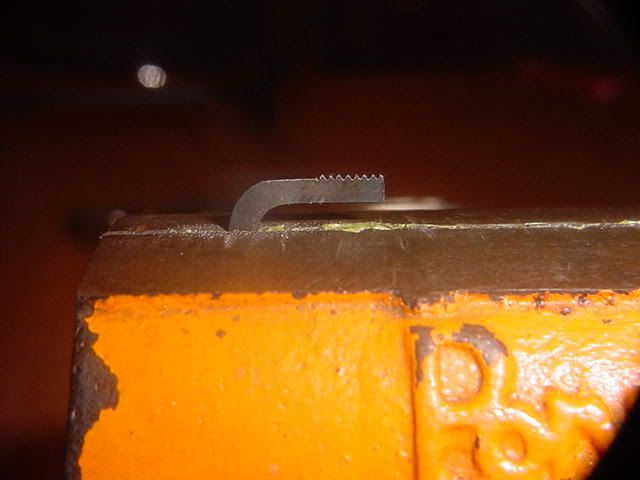
Now for the other end of the bristle, cut with a dremel or file a third of the width so that
the the lower round edge stops the bristle from going any closer to the first key pin.
Make 3-4 marks depending on how many teeth you want to have, using the triangular needle
file. File down each mark 3 or 4 strokes on each mark so the valleys are the same depth till
the teeth have a sharp pointy edge. Cut, grind or file remainder off to the first peak shown here.
*Note: Be sure to file a recessed area near the edge to allow the teeth to protrude and grip the
inside of the cylinder.
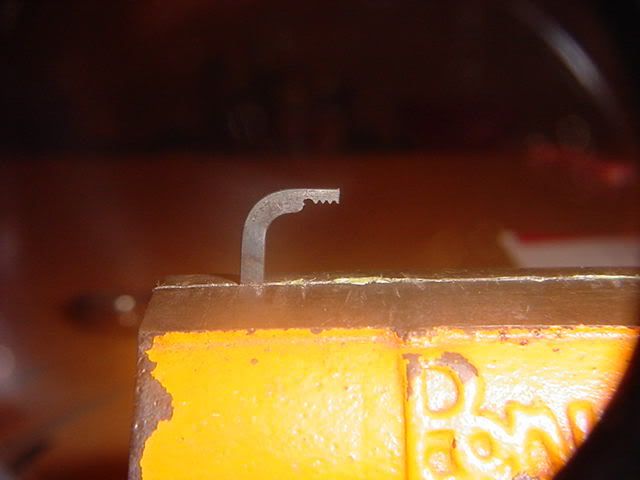
When done, sand with progressively finer grits of sand paper for a smooth shiny finish. You
should now have something that looks like this. *Note: The tool can be tempered if used with a heavy
hand or it can be left as is. I always temper my tools for long life and durability.
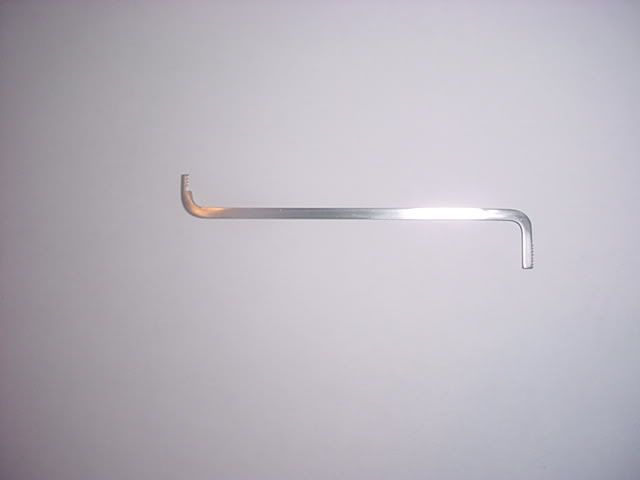
Hope you have enjoyed this How-To and that it helps. If there are any questions or comments, please
feel free to post them.
Kaotik