When it comes down to it there is nothing better than manual tools for your Lock pick Set, whether they be retail, homebrew, macgyver style. DIY'ers look here.
by ericm115 » 7 Aug 2006 23:45
So I have been trying to pick the control shear on a BEST SFIC (J keyway) with zero reliable success with more than two pins in the lock (with 3 it becomes 50/50 control/operating... which means my tensioner isn't working). The whole tensioner design has me baffled. I've been using the search function heavily over the last two weeks of my membership here, so I'm familiar with this: viewtopic.php?p=10840&highlight=#10840
I made a tension tool with tooth depth and spacing fitted for my core (I used the holes in the bottom of the plug as my guide). I am certain that my teeth do not penetrate beyond the control sleeve. Still, I am confused about this:
Notice in Fig1_A, with my tensioner in place (blue), applying tension in the normal fashion causes the tensioner to press against the right side of the plug. This creates a counterclockwise tension on the operating shearline (red), and, of course, a clockwise tension on the control line (green). (I know that Best core operating shearlines open clockwise generally, but I have some cores that open either way.) To remedy this, I suppose one could use the tensioner as seen in Fig1_B. You could just pull the tensioner straight to the side... with your funny looking hand...heh... This only puts tension on the control line as required, but this method doesn't allow very precise control over the tension. Not to mention it's just impractical for picking.
How about this design instead:
I've never seen or heard of this design before. I'm wondering if any of you have or if you think it would work. Fig2_A shows the tension wrench with a curved bottom with three (or more) circles (actually small cylinders) protruding that would fit the bottom of the control sleeve perfectly. The curvature would be the same and the hole diameter the same. This would lead to Fig2_B which clearly shows the desired tension applied solely to the control shear, and the standard method of applying tension using leverage for control.
To make one, I propose this process:
The differences in each successive step (A-D) are shown in blue while the removed material at each step is shown as a dotted black line. StepA->B: Carefully measure, mark, and file the protruding circles. This would need to be done with calipers and a hand file I would assume. StepB->C: Carefully measuring the inner curvature of the control sleeve, file the outside edges of the tensioner to the appropriate thickness (shown in red). StepC->D: Complete the smooth curvature to fit.
Ok ok... I've read enough posts to know how some of you think. The obvious response is, "Uh... try it and see." Fair enough. I suppose I will if the senior guys around here think it worth the effort - and it certainly would take some effort... I'm not particularly looking forward to it unless it has a substantial advantage over the conventional design.
Has anyone seen anything like this before? Do you think it would be effective? More importantly, do you think it would be worth the effort?
em
-
ericm115
-
- Posts: 112
- Joined: 13 Jul 2006 0:56
- Location: Columbia, SC
by ericm115 » 7 Aug 2006 23:46
eek. sorry for the monster sized pics. the file sizes are relatively small at least.... 
-
ericm115
-
- Posts: 112
- Joined: 13 Jul 2006 0:56
- Location: Columbia, SC
by Octillion » 8 Aug 2006 0:52
How do you expect it to secure itself to the control sleeve while applying torque? From what I see above, it won’t stay secure at all.
-
Octillion
-
- Posts: 350
- Joined: 19 Dec 2005 0:40
- Location: Connecticut
by ericm115 » 8 Aug 2006 2:01
If you look at this picture, it shows the difference between the proposed method and the conventional method:
In situation A, you only have 8 contact points between the control sleeve and the tensioner (though they aren't so much points as "edges"). In the side view, its obvious that one mishappen edge (marked with the star) out of 8 contact "points" will cause the tensioner to be pushed up and out of the hole under applied tension.
In situation B, you have substantial surface area contacting the edge of the hole in the control sleeve. Even if one of the circular protrusions is mishapen as shown in the starred portion of A, the friction due to the no-longer-negligable contact area between the tensioner and the control sleeve will fight the tendency to slip out of the hole.
The closer the fit between the circular protrusions and the holes, the better the grip. In fact, I think if the protrusions had to be worked into the holes because the tolerance was tight (ie: it fit like a glove) you would be able to put plenty of tension on the tensioner without the protrusions coming out. For example,
That's only a two dimensional representation though. In reality, those two contact points would be half circles around the protrusion (which is still more contact area than with the conventional tensioner.)
Not to mention, the control sleeve isn't spring loaded, so if you wanted to carefully back off the tension, being able to apply very tiny forces in the opposite direction would be much easier with the proposed design... assuming it would actually work..
These are simply my thoughts on this and their validity is in no way guaranteed.
em
-
ericm115
-
- Posts: 112
- Joined: 13 Jul 2006 0:56
- Location: Columbia, SC
by LockNewbie21 » 8 Aug 2006 4:23
Well i will give you credit on your presentaion of the proposed idea, its brilliant as most just do this to show a wrench L____
Your idea can work, you have to get the angels just right.
Just a thought make a double ended wrench for top and botttom of plug if securing it in hole's is a problem.
Either that just practice the old way, i am talking to amnikron about some sfic's from best, i will have to take a look and see what i can rig up. I am sure theres a way to have them flush, but there isn;t much i can do with a cylinder.
[deadlink]http://i60.photobucket.com/albums/h17/Locknewbie21/LockNewbie21Sig.jpg[/img]
-
LockNewbie21
-
- Posts: 3625
- Joined: 21 Feb 2006 2:26
- Location: The Keystone State
by Octillion » 8 Aug 2006 11:06
I doubt that will work. The control sleeve is rather shallow, so it’s just going to pop right out as soon as torque is applied. Good effort, but it needs more thought.
-
Octillion
-
- Posts: 350
- Joined: 19 Dec 2005 0:40
- Location: Connecticut
by I Pik U » 5 Oct 2006 11:15
Just yesterday I needed to pick a Best SFIC mortise cylinder, to remove the core. Using the Peterson IC core plug removal tension wrenches, like the one in the link in ericm's first post here, I was able to pick the plug at the normal shear line, but not the core removal shear line.
I got to thinking then for a solution. I suggested to my co worker, why not drill a small hole in the side of the cylinder housing where the core removal lug is located. Just deep enough to reach the lug. Then with a poke tool and an elastic wrapped around it and the cylinder body to apply force/tension on the lug, we again picked at the cylinder using the Peterson tension wrenches and were succesful in picking the core removal shear line in short order!
We could then remove the SFIC core from the cylinder body and rekey it to our needs.
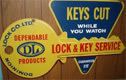 Been playing with locks since '68.
-
I Pik U
-
- Posts: 304
- Joined: 8 Sep 2006 11:56
- Location: Ontario, Canada
by I Pik U » 5 Oct 2006 11:20
I do like Ericm's design above. I would wonder if it does a better job than the Peterson's tension wrenches, as I was able to pick the plug to turn, but not the removal shear line.
The Peterson wrenches have a tendancy to rotate in the keyway and apply tension to the plug as well as the removal sleeve. If by Ericm's design the tension was only applied to the removal sleeve, that would make a better tool.
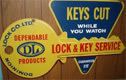 Been playing with locks since '68.
-
I Pik U
-
- Posts: 304
- Joined: 8 Sep 2006 11:56
- Location: Ontario, Canada
by ericm115 » 5 Oct 2006 12:31
Well, I have a control sleeve just sitting around. If I knew anything about casting, I could just cast a mold of the sleeve somehow and make a perfect tensioner.
Anyone have any ideas about how to cast something strong enough to be a tensioner?
em
Original image copyright Toaplan. This qualifies as "fair use" under US Copyright law.
-
ericm115
-
- Posts: 112
- Joined: 13 Jul 2006 0:56
- Location: Columbia, SC
by Shrub » 5 Oct 2006 12:47
Wow thats a whole can of worms right there,
You would be easier cutting the sleave up and silver soldering an arm on it but i havent paid much attention to these locks nor the systems as i dont come across them so it may not be what your after,
-
Shrub
- Moderator Emeritus
-
- Posts: 11576
- Joined: 23 May 2005 4:03
- Location: uk
by Octillion » 5 Oct 2006 17:04
Rather than silver soldering and making a mess of the thing, you could simply superglue the plug to the control sleeve. When the glue sets, pick the core out, then clean the core with acetone.
-
Octillion
-
- Posts: 350
- Joined: 19 Dec 2005 0:40
- Location: Connecticut
by eric343 » 5 Oct 2006 22:30
Except it would be real easy to superglue the control sleeve to the shell at the same time...
-
eric343
-
- Posts: 569
- Joined: 11 Dec 2003 19:51
by Octillion » 5 Oct 2006 22:35
Well, true, depending on the orientation of the lock. If it is installed on a door for example, this may not work, but a padlock or uninstalled lock can be oriented such that careful application won't get any glue in the shell.
-
Octillion
-
- Posts: 350
- Joined: 19 Dec 2005 0:40
- Location: Connecticut
by SteveOXIII » 8 Oct 2006 8:18
I found it once on here, but I don't know where.
Those picks depend on the thickness, you have to apply tension to the control section without distubing the rest of the lock. From what I've read before they sell the tension wrenches based on the model of the lock, so maybe try more downward pressure as opposed to sideways?
If I find the post [It was a pic set of different lock types] I'll repost here.
-
SteveOXIII
-
- Posts: 23
- Joined: 1 Oct 2006 0:07
- Location: NW Indiana
Return to Lock Picks
Who is online
Users browsing this forum: No registered users and 2 guests
|