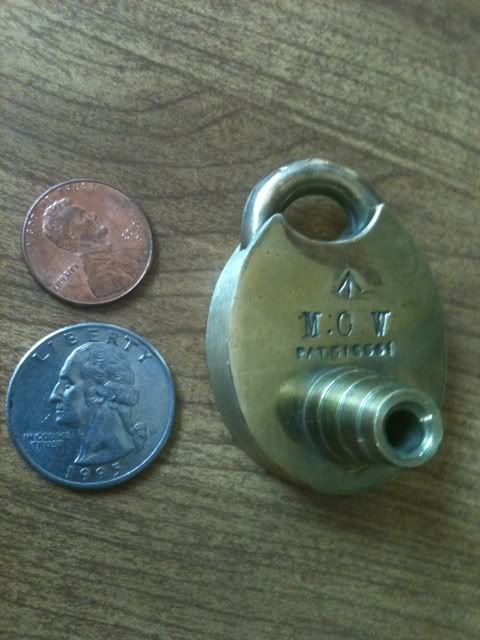
First, made a high tech measuring tool from a bobby pin.
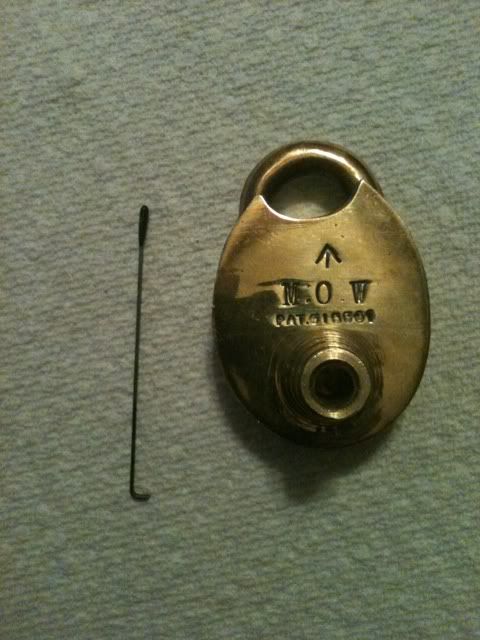
Slide the hook end down into the keyway. The measurements needed are the full depth of the keyway, the top and bottom of the slot at 9 o'clock and at 6 o'clock. When the hook gets to those measurement points, use tape level with the top of the keyway to mark the measurement.
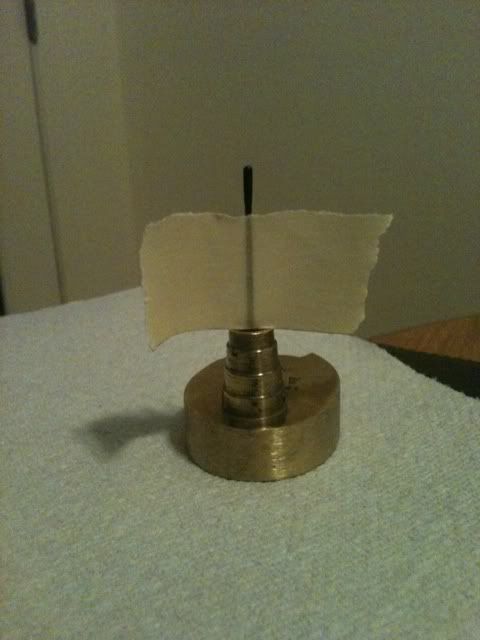
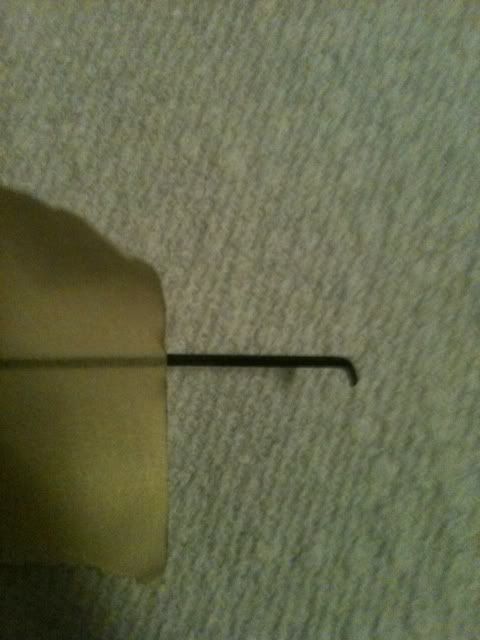
Then use a micrometer to measure it. If measuring the top of the groove, measure to the inside of the angle of the hook. If measuring to the bottom of the keyway or bottom of the groove, measure to the outside end of the hook.
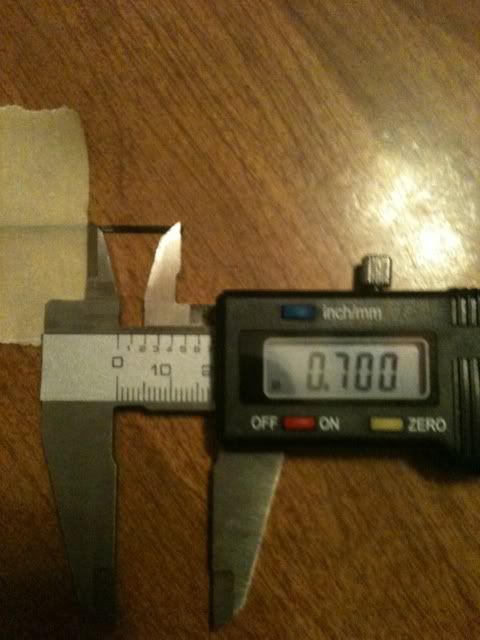
These are the measurements...
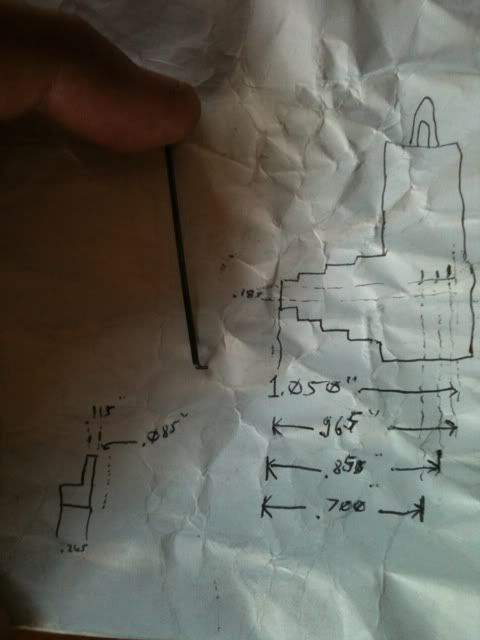
These are the primary components of the key. The shaft of the key is made of aluminum because that is the widest diameter tubing I had in my collection. And the inside of the shaft is brass tubing, because it needed to be stronger. Used epoxy to hold the inner and outer tubing together. The movable part of the key is made from windshield wiper spring. Drilled it with a diamond bit dremel bit to slightly over 1/16". The pivot pin is brass. Drill holes through the tubing for the pivot pin. Cut the slot in the tubing with a dremel tool, clean up the edges with a needle file.
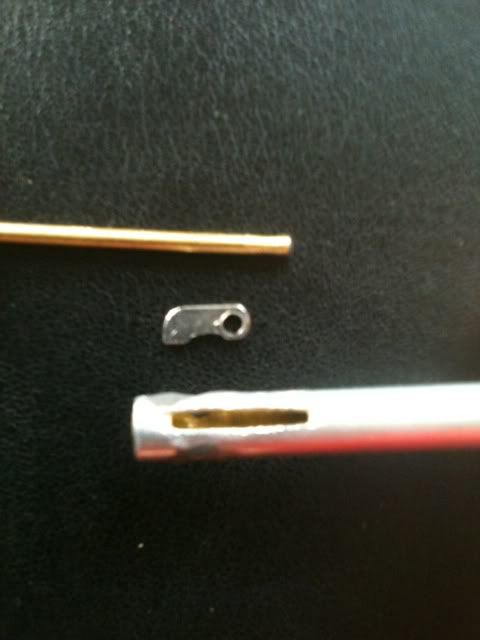
Trial fit the parts, and make sure that the movable part swivels completely freely. If it binds up inside the lock, you are screwed! So be sure it moves freely. When it moves freely, epoxy the pivot pin in place.
Do not hammer the pivot pin with a small hammer like a rivet - it will bend, and you will have to drill it out and make another pivot pin. This is experience speaking.

Before the epoxy dries, again make sure the moving part moves freely. This key moving element is gravity operated. Did not think it would work, but the patent drawings don't lie. So make sure it pivots easily.
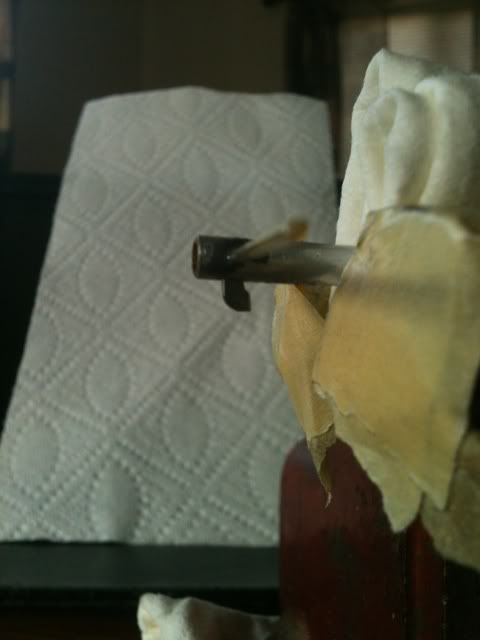
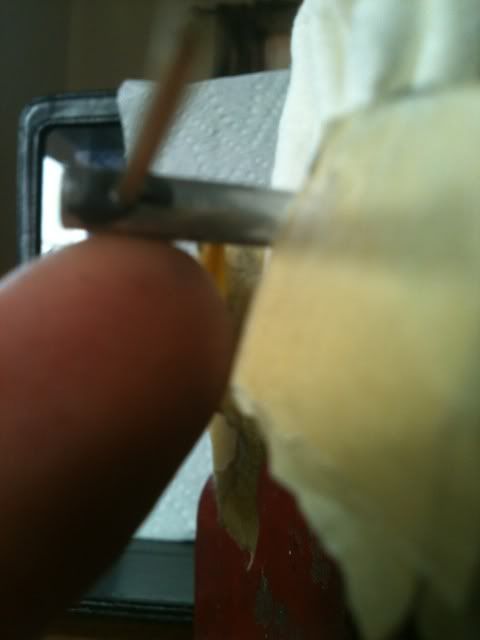
Once the epoxy (I used JB Weld) was dried and hardened, used a dremel with a cutoff wheel to cut the pivot pin off on both sides. Then used a needle file to clean up the sides. Then it should look like this...
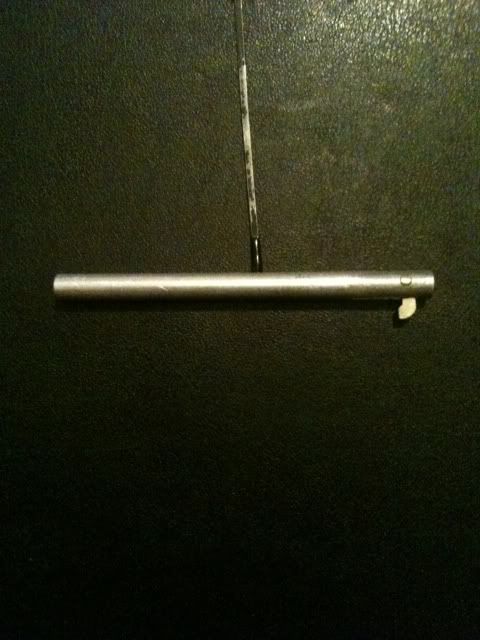
With the moving element inside the tubing... (fgarci03, get your mind out of the gutter!)
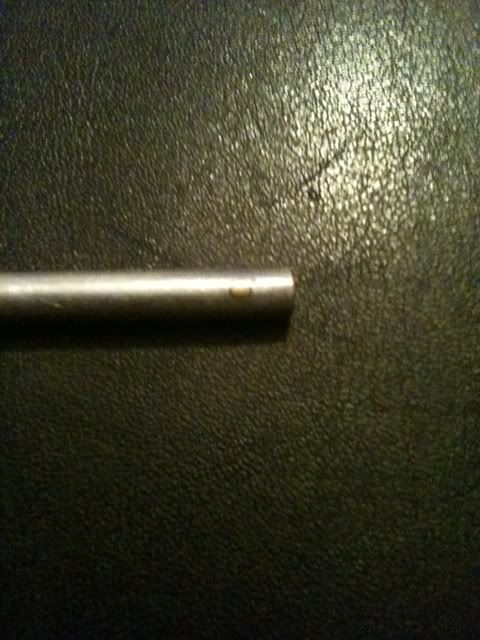
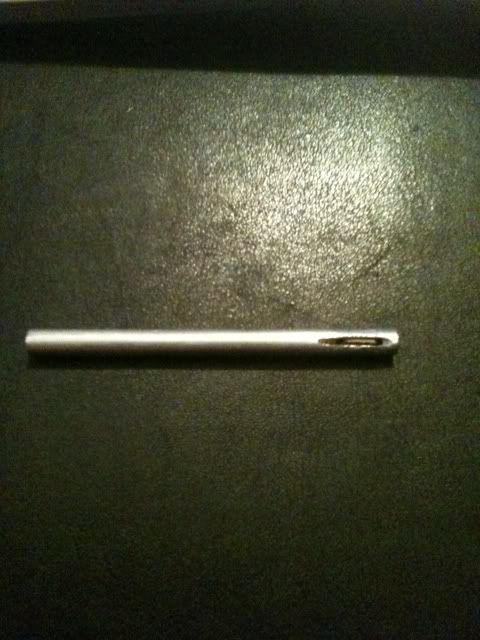
Sizing some aluminum stock for a bow.
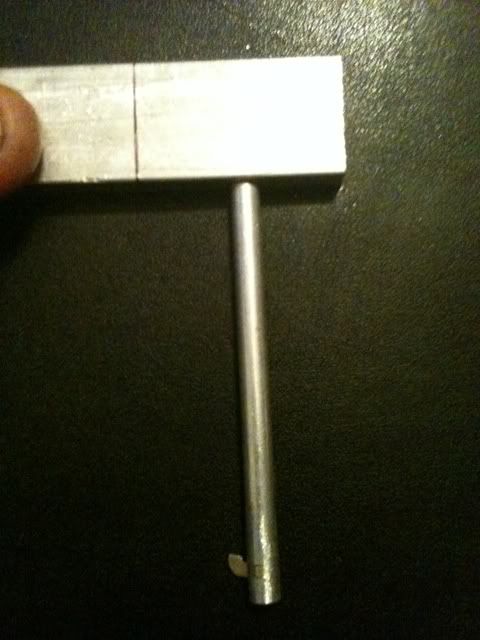
And marking for drilling to insert the key into the bow.
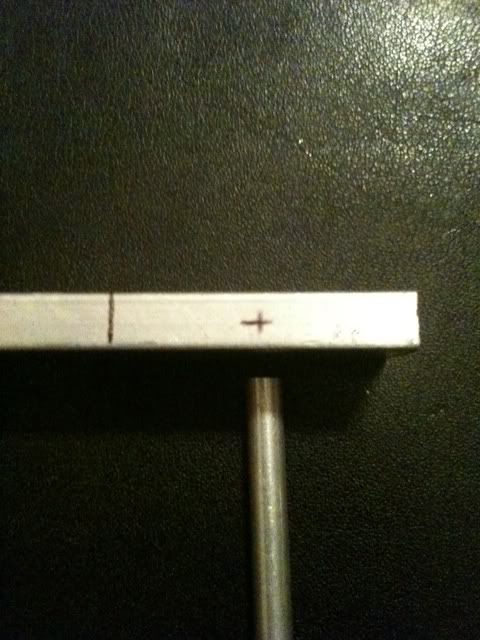
Drilled the hole - 1/16" for a pilot hole, then worked up to 3/16".
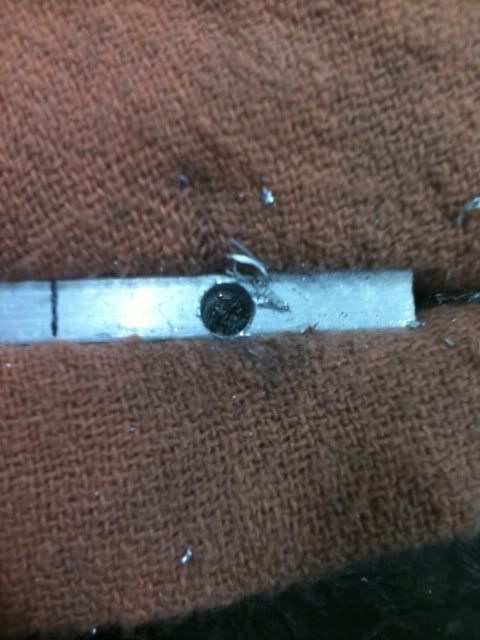
Shaped the bow, rounded the edges. Roughened the sides of the key shaft where it will be glued into the bow.
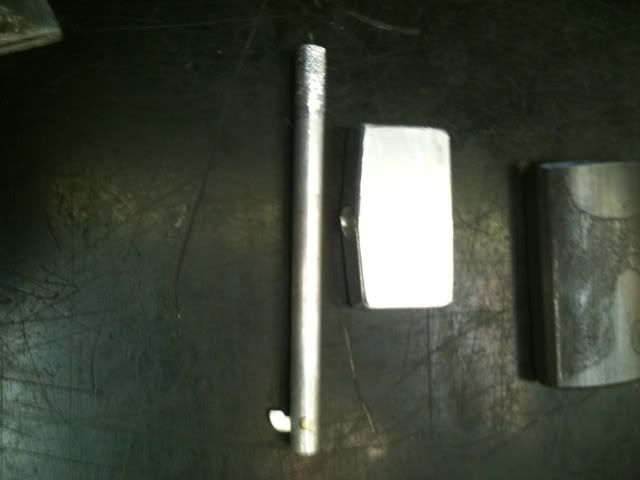
Used JB Weld epoxy to bond the bow to the shaft. Let it set overnight to cure the epoxy fully.
The resulting key and lock!
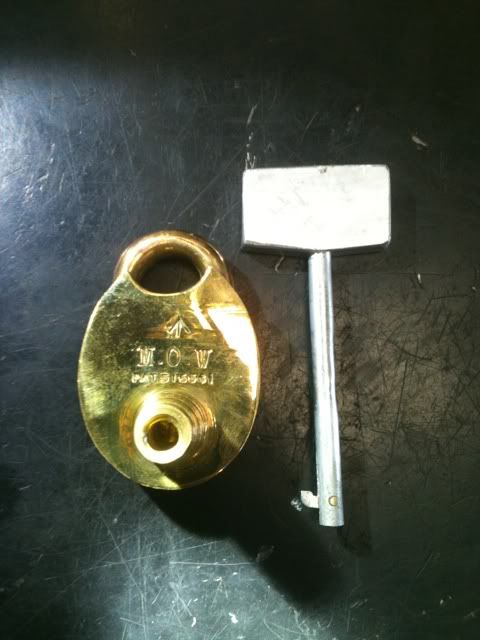
Gordon