Br0keN wrote:How did you make those locks? I would imagine that you would need to make the movable shear line part out of a separate piece of brass or steel.
First you need two cylinders just to make one.
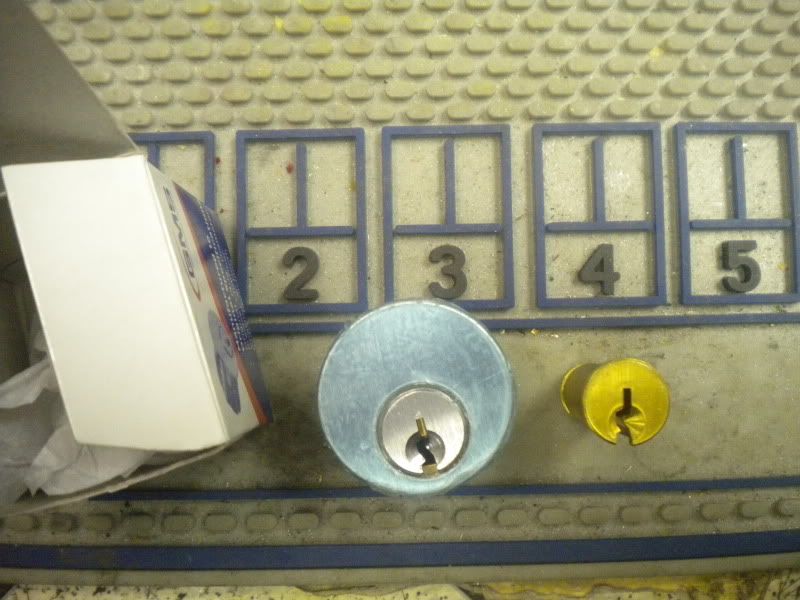
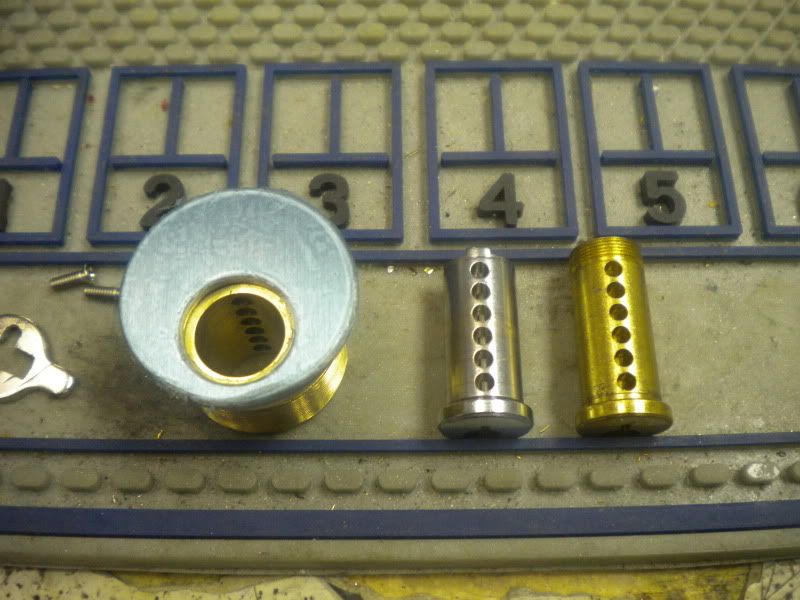
To mill away the top part of the cylinder to support the sliding piece. I use a separate housing that has been cut apart. This allows me to clamp it in the key machines jaws and mill it away. I tend to eyeball things, so I don't have any exact measurements. I just set the cutter at a depth that seems right, lock it in place. Then lock in the X (or is it Y) axis? And cut forwards and backwards. Then readjust the x axis and cut forwards and backwards etc...
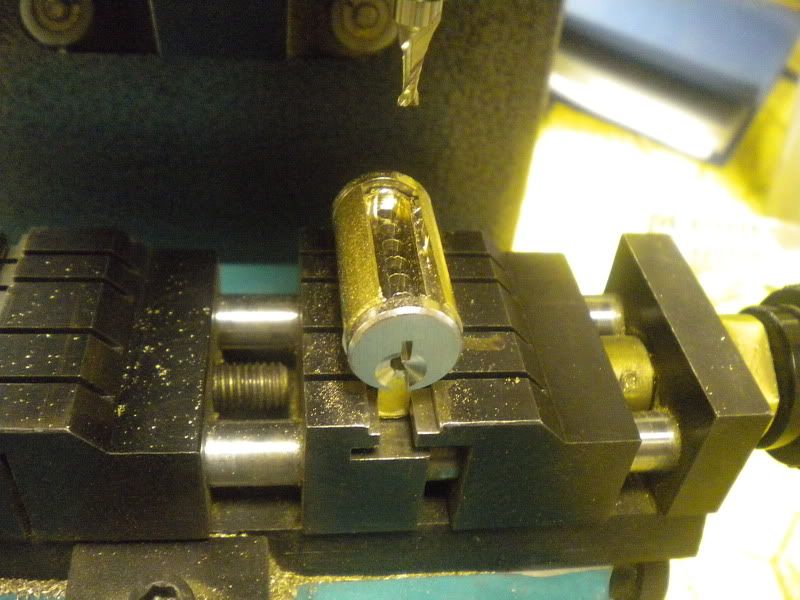
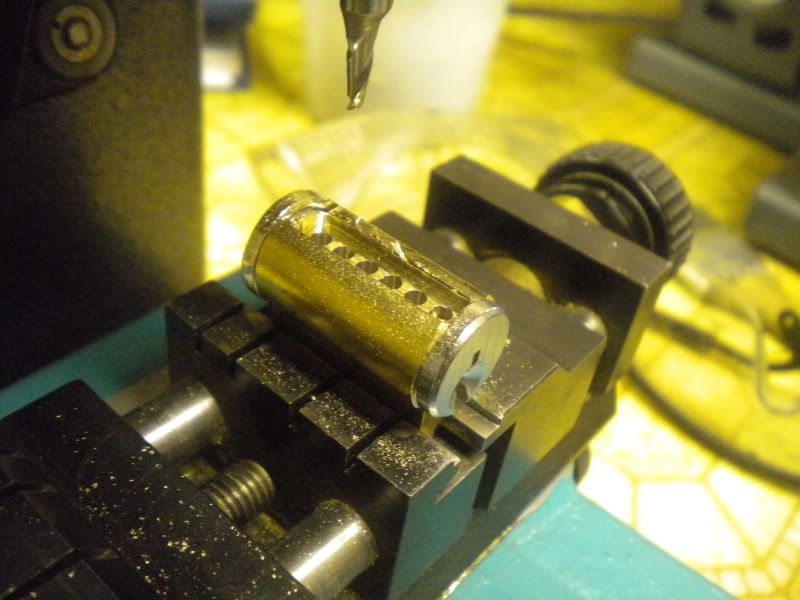
A little deburring and cleaning and this is what's left!
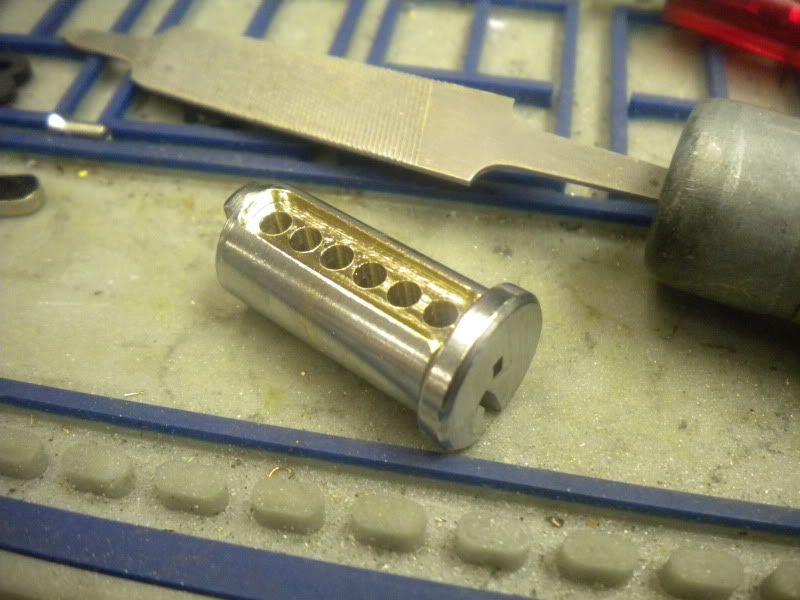
I use a Craftsman Multi-tool to save a lot of time on cutting out the slider piece out of the other cylinder.
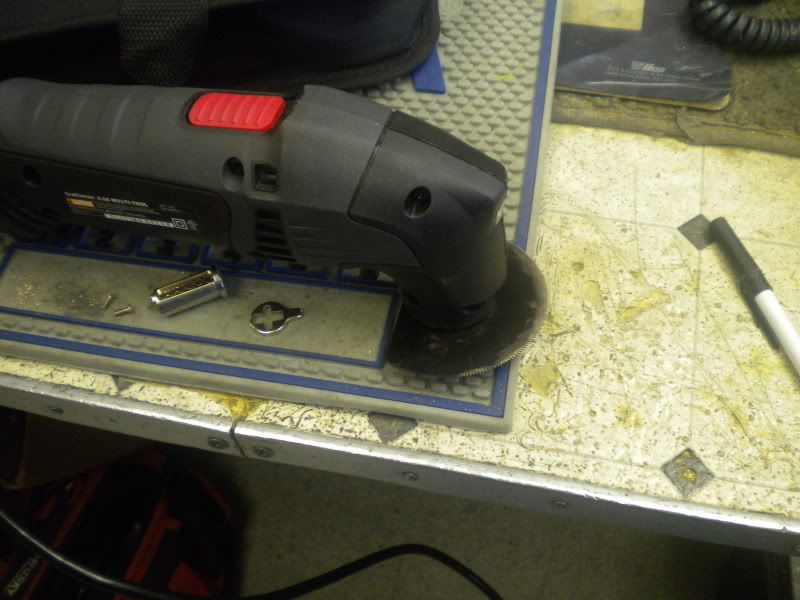
Clamp the cylinder in a vice jaw like so.
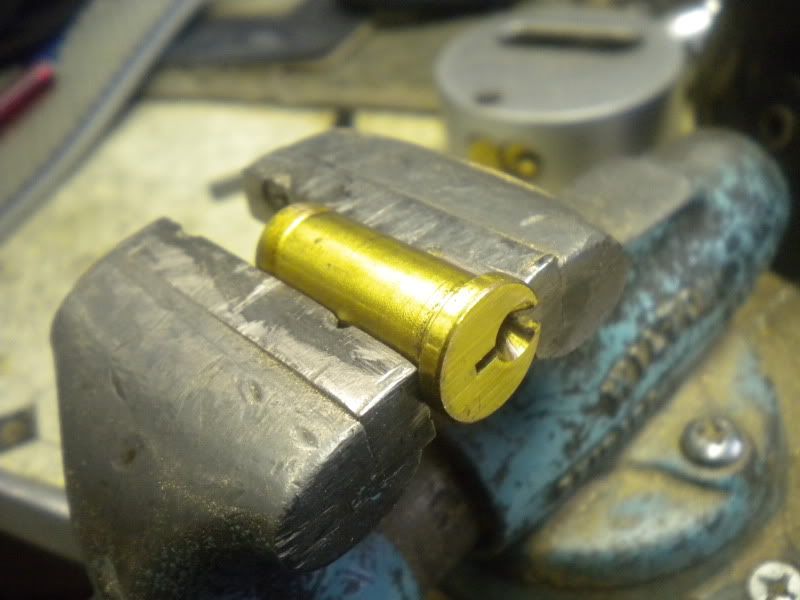
Cut a groove in it.
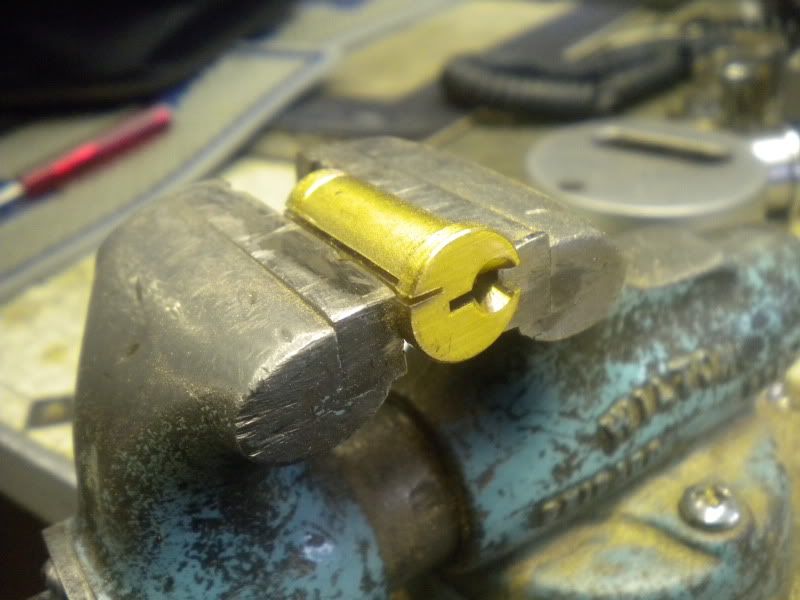
Turn the cylinder around and cut another groove.
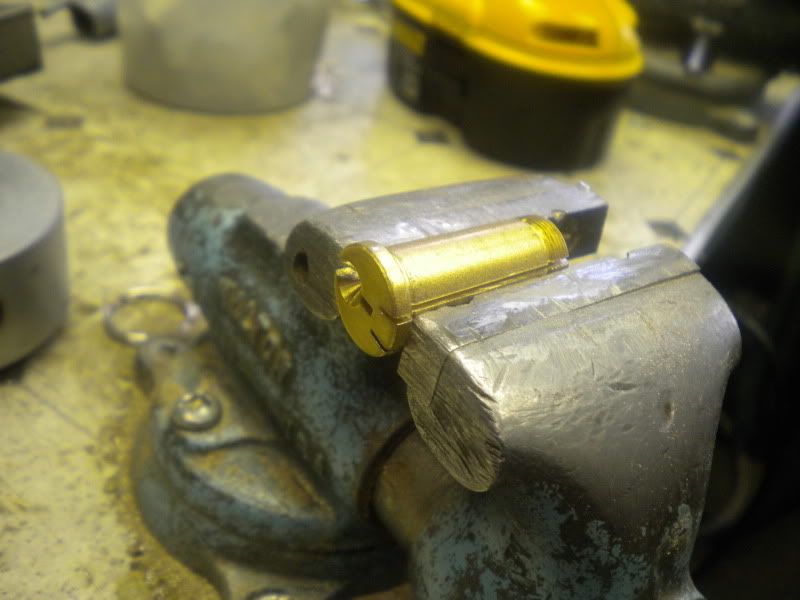
Put the cylinder in the vice like so and cut a groove before and after all the chambers. Then start cutting the top off.
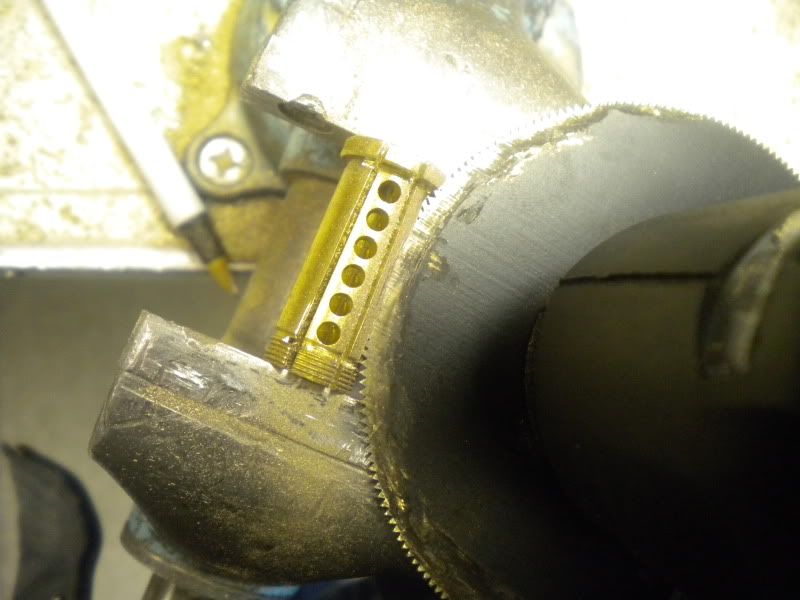
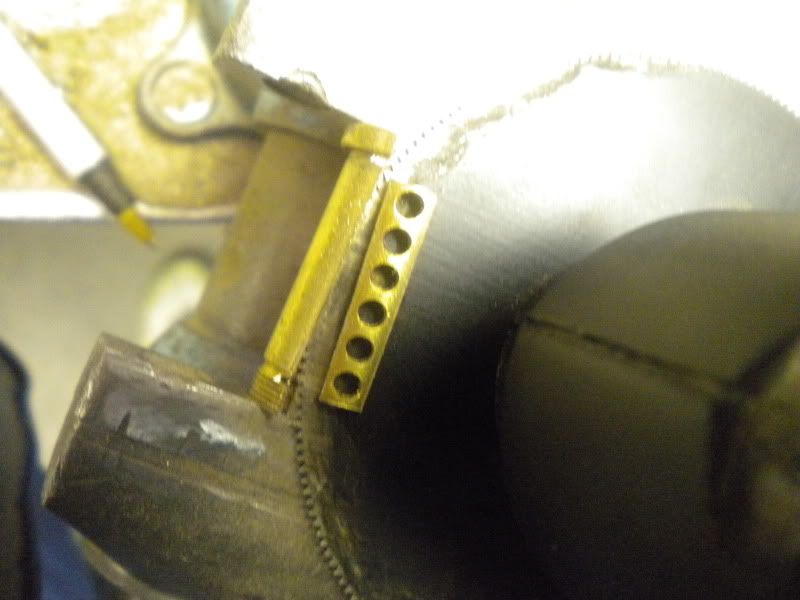
Once you have the piece cut off. It shouldn't fit into the milled out cavity yet. If anything you want it over sized so it can be filed down to perfection (or something close).
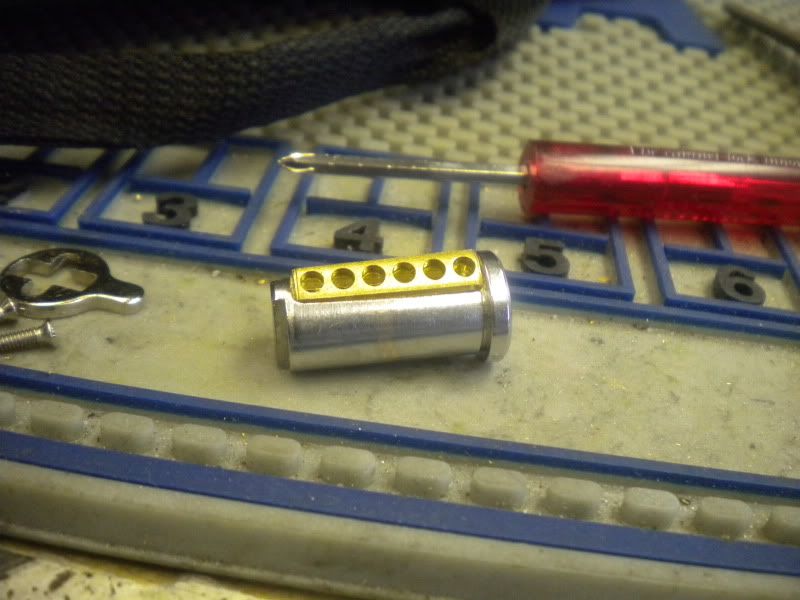
After filing down the corners and sides a little bit it should fit a little better. But should still be too tall.
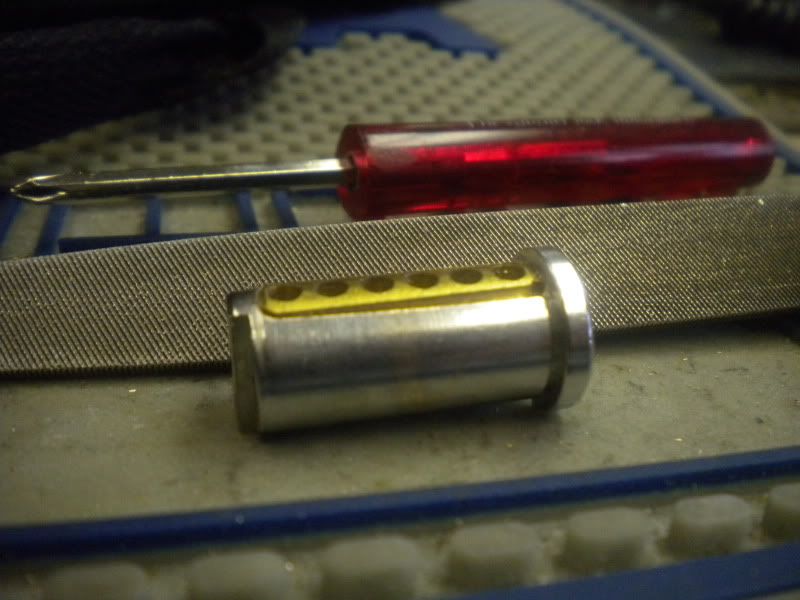
Then next trick is to file down the entire thickness of the slider to the correct thickness. I've learned the easiest way to do that is if it is held in place while filing. So I take to pins that I'm not going to use, press them into the slider. The slider isn't deburred at this point so if you can get them in they will stay long enough for you to clamp them in the vice.
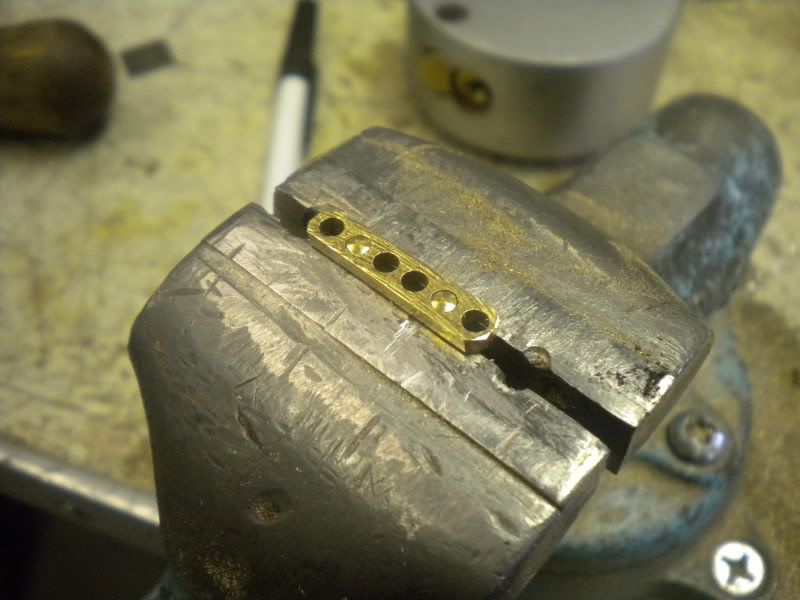
Make sure you can pull it off the pins at anytime so you can check how close to perfection it is at any time.
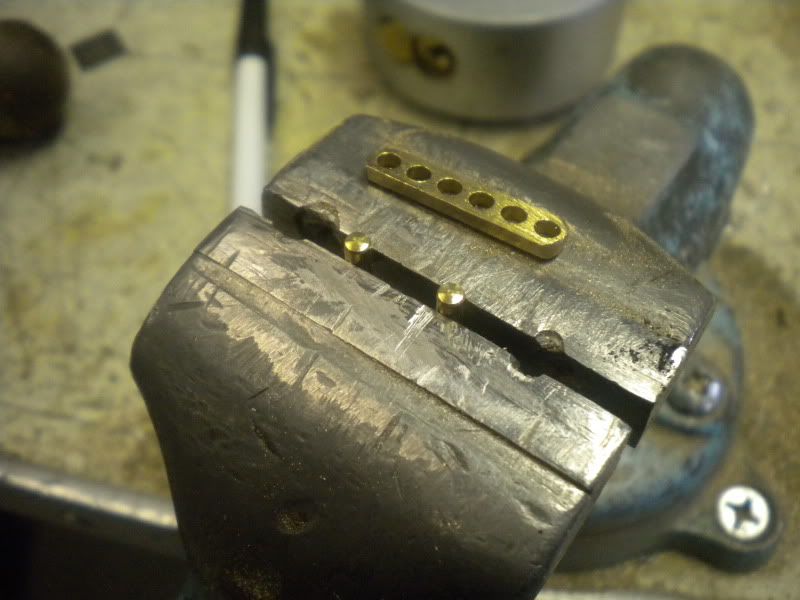
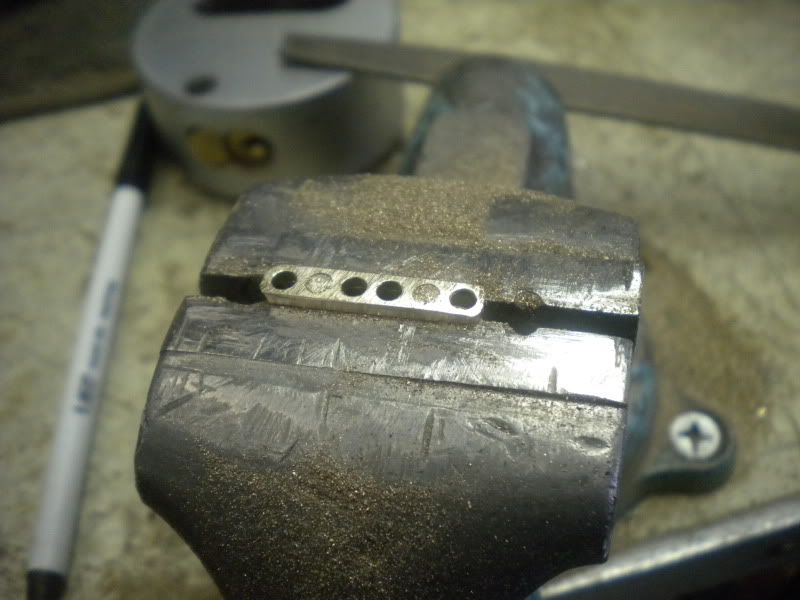
Once it's perfect, the slider should be able to move around (left/right) with ease while inside the housing.
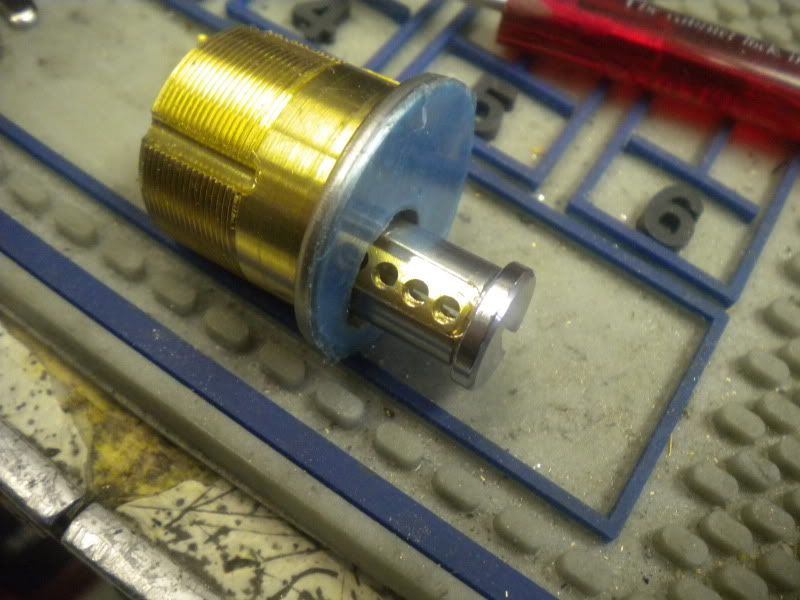